From Connected Worker to Connected Intelligence at Georgia-Pacific
Add bookmark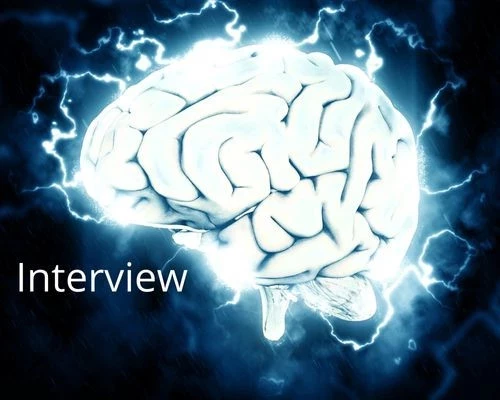
Georgia-Pacific is one of the world’s largest manufacturers of pulp, packaging, tissue and building products. The company has over 30,000 employees in 180+ locations worldwide. But a few years ago, the company recognized that it had a problem: a large proportion of its workforce would soon be retiring.
Since then, it has embarked on a journey – both technological and organizational – to address the looming knowledge gap, embed more predictive and intelligent capabilities into its operations and improve its operational resilience.
In this interview, Ron Norris, Director of Operations Innovation at Georgia-Pacific discusses what the company has done, lessons learned along the way, and where they’re going next.
Diana Davis, Industrial Transformation Network: I understand that you embarked on a Connected Worker strategy a few years ago. Can you tell me about what you’ve done?
Ron Norris, Georgia-Pacific: It's not so much what we've done. It's what we've recognized that needs to be done and forging a way to make that happen.
A couple of years ago, we saw that our ability to hire new workers on the scale that we've been able to hire them previously was starting to slip.
With paper mills, you want to be where the raw materials are and that means out in the woods. You're not near major cities. Our challenge is that a lot of the younger millennials and Gen Xers are moving to cities because that’s where they perceive that things are happening and it's a cool place to be.
The other challenge is the amount of our workforce that has and will be soon retiring. We did a survey back in 2015 that found that a sizable percentage of our workforce was going to be over 65 years old by 2023, and many of these employees have been with us for 20, 25 and 30 years.
You can't replace a large percentage of your workforce with somebody that's just coming out of school. How do we train them? There's no way to take 35 years of knowledge and replace it right away.
We had to adapt and be different. Things still had to get done, and we knew that we couldn’t change that. But what we could change was how our workforce participates in how those things get done.
We wanted to find a way to capture subject matter expert knowledge quickly; the new workforce that’s coming in won’t have time to learn it the traditional tribal way.
The new team members needed a quick way to learn and get answers.
That’s why we developed what we call the CSC, which is our Collaboration and Support Center. We staff the CSC with subject matter experts to support our diverse businesses.
The SMEs are only a click or call away to help the facilities when they have a question or issue.
The CSC also gets all the data from the mills, and it’s also staffed with very smart data scientists. Before a maintenance technician encounters a problem, such as a vibration on a certain bearing or a machine making a weird noise, the CSC is now a step ahead. They're monitoring these things and letting us know ahead of time that there's a problem that we need to go look at.
We also wanted to improve our upskilling and reskilling capability.
In a lot of companies, you're hired as a technician at a certain level. But what does it take to get to the next level? If nobody has the time to help you learn, how can you get better? How do you advance? We wanted a system that helps you learn and tailors your education.
Diana Davis, Industrial Transformation Network: It sounded like you needed a lot of data in place to even get started, like was data one of those key starting points. How did you get started?
Ron Norris, Georgia-Pacific: When we started what everybody's calling industrial transformation or Industry 4.0 there was no book on how to do it. We just saw a problem – that a sizable percentage of our workforce would be retiring – that we needed to solve.
How were we going to be able to operate in the method that we needed to operate? Creating the CSC was one of the first steps.
We also started working on predicting machine failure before it happens. The only way we knew how at the time was through Excel worksheets, which now sounds totally old-fashioned.
But that was how we had to do it because there were no AI programs built for that usage. We had to get a way for our people to learn and we had to get data from the machines coming into our CSC.
What we found out first was that our data wasn’t that great: it was everywhere, it was archived, it was compressed, and honestly, a lot of it was terrible.
We needed to figure out how to get better data out of our machines.
We’re at the point now where the CSC has computer programs – along with other capabilities - that can help them monitor the health of each part of our huge facilities.
Before we started working on Excel spreadsheets when something broke, that's when you found out that it had a problem. At that point, your production is down and you’re scrambling.
When your production is down, that’s a big deal because those facilities are made to put product on a truck and get that product onto shelves so that consumers have access to the things that they need: their toilet paper and paper towels and Dixie Cups and boxes and plywood and whatever else they need.
We thought we were great with Excel spreadsheets when we first were able to go from not knowing anything to being able to predict about 15 minutes in advance that something was going to break. Now it’s developed to where we're days and weeks ahead that those things can be predicted.
Diana Davis, Industrial Transformation Network: What would you say were your biggest lessons learned over the last couple of years as you've done this work?
Ron Norris, Georgia-Pacific: It’s daunting to get started with all of this. It's a big change management issue.
We’ve got a company that's over a century old and although we’re a very progressive company, how we do things are kind of ingrained.
The important thing we’ve learned is not to let what you know get in the way of what you're about to learn.
Sometimes we would think of something and then somebody would dismiss it because it had supposedly been tried it before, and it didn't work.
The problem is that you may have tried something eight or nine years ago when the technology didn’t exist in the same way. Then you get locked into what you know and what you think. If you think this will never work, you’re not going to do it. And just because it didn’t work in the past doesn’t mean that it won’t work now.
Diana Davis, Industrial Transformation Network: Where are you going next with connected worker?
Ron Norris, Georgia-Pacific: Connected worker is an ongoing part of our roadmap.
We have over 150 manufacturing sites and several years back we gave iPads to our workforce in the factories and mills.
If you've ever been into a giant manufacturing facility like a paper mill, you’ll see huge machines. In a typical paper mill, there are about six or seven machines that are each about 400 feet long. There is a lot of inherent noise in these environments – both auditory and other distractions.
You don’t want to give your workforce tools that add to the level of distraction.
If you supply an iPad with 25 apps on it, each app with its own alerts, how does your workforce prioritize all the information?
We’re working on a cognitive-based AI system that can help them do that. It helps them cut through the clutter. Here's what needs to be prioritized. Here's what needs to happen right now. Here's what you need to watch out for, and, and here's how we approach the next task that we have.
That’s our next step on connected worker: to help the workforce prioritize what needs to be done through artificial intelligence. Again, we’re not changing what needs to get done. We’re changing the way people participate in what needs to get done.
To do this, we’re not just using traditional AI, but an intelligent model of AI that's taught not only with data, but by using knowledge that comes from the subject matter experts that have worked in the facility.
If our workforce has a problem, they can tap into the knowledge of the workforce that has been here. The AI will constantly update itself when new products or new projects or new ways to manufacture as they come along.
Diana Davis, Industrial Transformation Network: What are you looking forward to at our Connected Worker Summit that you’re speaking at, and what would you say to someone coming to the event for the first time?
Ron Norris, Georgia-Pacific: I like to talk to companies that are experiencing similar problems and find out how they are attempting to solve those problems. I believe that if you are coming to an event like this, you want to leave with some “go-to” items.
In the past, I was always interested to see if there were possibilities for collaboration. Are there other companies out there with similar challenges where we could work together and cut innovation time and risk? That’s one of the things that new attendees could be focusing on.
If you can share the knowledge and cut down the time to get things done, then you can share the rewards and help other people at the same time.
Interested in learning more?
Ron Norris will be speaking at our Connected Worker Summit taking place November 15-17 in Chicago. Join over 200 of your peers in intensive workshop sessions, focused learning tracks, discussion groups and interactive panel discussions on a 3-day program that will offer inspirational ideas and solutions for wherever you are in your transformation journey.
If you want to optimize the performance of your people and drastically improve productivity across your operations, download the agenda now to find out how you can leverage connected worker technologies to improve operational efficiency, training, asset management, quality and safety. Download the agenda here.