The Circular Economy and Decarbonization — Closing the Loop on Resource Use
Add bookmark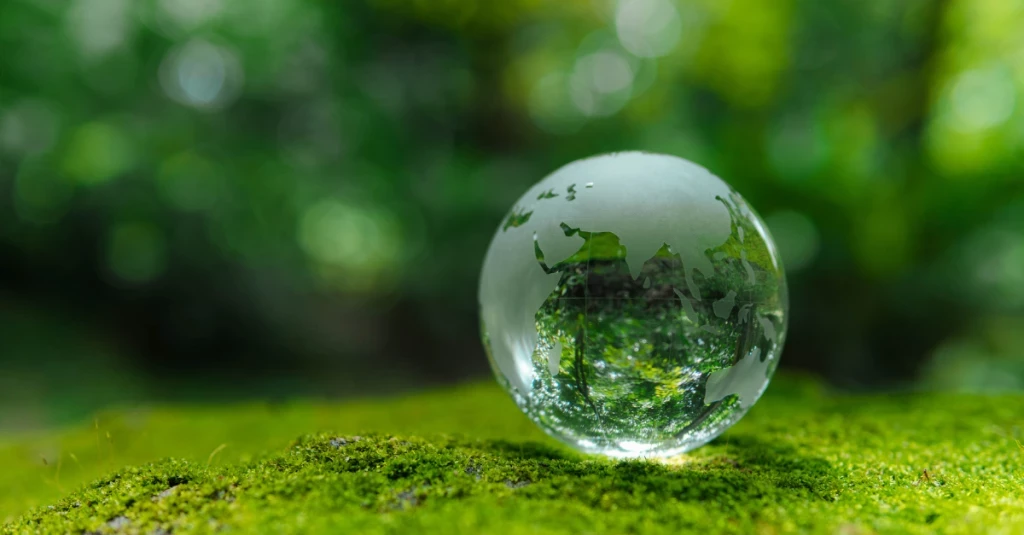
Industrial sites run on energy-hungry heat, high-volume materials and tight schedules. Every fresh ore or resin shipment that comes in eventually leaves as waste or hidden emissions. Closing that loop by keeping materials in use instead of buying, burning or sending them to landfills lets companies cut carbon and costs in the same move. This article examines how a circular mindset speeds decarbonization and what sustainability leaders can do next.
Decarbonization — The Industrial Imperative
In 2022, heavy industry pumped about nine gigatons of carbon dioxide into the atmosphere — roughly one-quarter of all energy-related emissions. Global agreements demanded a sharp U-turn. The Paris Climate Conference aimed to keep warming to 1.5 degrees Celsius by 2100. The Intergovernmental Panel on Climate Change warns that total carbon pollution between 2012 and 2100 must stay under 400 billion tons to stand a two-thirds chance of hitting that limit.
Governments are moving — at the 76th UN General Assembly, China pledged to peak emissions before 2030 and reach carbon neutrality by 2060. Markets are also shifting. The Science-Based Targets initiative offers the leading rulebook that lets firms align their climate goals with a net-zero world by 2050 at the latest. According to PwC’s Second Annual State of Decarbonization, 37% of companies raised their climate ambition in 2024, while only 16% dialed it back — proof that momentum is edging forward sector by sector.
The Circular Economy in an Industrial Context
A circular economy asks three simple questions — What if materials never go to waste? Can products stay in use longer? Can natural systems recover instead of degrade? Unlike the old “take, make, discard” model, circular thinking treats every item as a future input.
Real-world snapshots make the idea tangible:
- Automotive rebuild programs harvest gearboxes and electric motors for second-life sales
Aluminum smelters turn shop-floor scrap back into new billets
Cement kilns blend in ground demolition rubble to cut fresh clinker use
Keeping products in circulation can lower carbon emissions compared to extracting resources to constantly make new items that will only get thrown out again. For heavy industry, that shift reduces landfill fees and exposure to volatile commodity prices.
Barriers and Enablers — What’s Holding Industry Back?
Why isn’t every plant circular already? Hurdles include capital-heavy equipment upgrades, patchy waste-material streams and legacy metrics that reward throughput over reuse. The transition also calls for an upskilled workforce — process engineers need expertise in material tracing and reverse logistics, not only throughput optimization. Lenders still view circular upgrades as riskier bets, inflating financing costs and slowing project pipelines. Procurement rules in many sectors default to the lower upfront price, weakening demand signals for recycled content.
On the bright side, policy tools are maturing — including recycled-content mandates, carbon pricing and accelerated depreciation for low-carbon assets. Digital product passports and better material tracking platforms make quality scrap easier to match with hungry mills. Standards from groups like the Science-Based Targets initiative also give leadership teams a yardstick for progress.
What Sustainability Leaders Can Do
Circularity and decarbonization succeed faster when they follow the same roadmap. Leaders can start with these practical steps.
- Map the material footprint: Trace where each ton of input comes from, how long it stays on-site and where it ends up.
Design for disassembly: New products and equipment should come apart easily so metals, plastics and composites reenter the loop - Digitize the loop: Use IoT sensors and AI to predict scrap quality and schedule preventive maintenance that extends asset life.
- Pilot industrial symbiosis: One company can share heat, water or by-products with neighboring plants to turn waste into feedstock
- Align targets and finance: Publicly adopt SBTi-approved goals, then tap green bonds or sustainability-linked loans that reward circular economy milestones
Transitioning From Waste to Worth
Circular thinking transforms yesterday’s waste into tomorrow’s profit — and today’s carbon savings. With global climate budgets tightening and investor scrutiny rising, industrial leaders who close material loops now will secure cleaner inputs, steadier costs and a stronger social license to operate. The next decade will separate pioneers from laggards as policy, pricing and technology converge around closed-loop models. Those who delay risk locking themselves into linear habits that the market — and the planet — can no longer afford.